Learn about CATIA, a CAD software program used for parametric modeling, and how it can improve automated processes. Automation is a process of embedding decision making into inanimate objects. Here, objects can be physical (hardware) or virtual (software). About Parametric Drawing and Constraints AutoCAD As the 3D features in AutoCAD are not true solid models, the selection of 3D constraints that can be created in AutoCAD is a limited. Dependent on the type of constraints you need, many users find it much easier to work with either Inventor or Fusion 360 which are designed this.
Developer(s) | PTC |
---|---|
Initial release | 2011; 10 years ago |
Stable release | |
Operating system | Windows |
Available in | English, Chinese (Traditional), Chinese (Simplified), French, German, Italian, Japanese, Korean, Spanish, Polish, Russian |
Type | CAD design software |
License | Proprietary |
Website | ptc.com/en/products/cad/creo/ |
Creo is a family or suite of Computer-aided design (CAD) apps supporting product design for discrete manufacturers and is developed by PTC. The suite consists of apps, each delivering a distinct set of capabilities for a user role within product development.
Creo runs on Microsoft Windows and provides apps for 3D CAD parametric featuresolid modeling, 3D direct modeling, 2D orthographic views, Finite Element Analysis and simulation, schematic design, technical illustrations, and viewing and visualization.
Creo Elements and Creo Parametric compete directly with CATIA, Siemens NX/Solidedge, and SolidWorks. The Creo suite of apps replace and supersede PTC's products formerly known as Pro/ENGINEER, CoCreate, and ProductView. Creo has many different software package solutions and features. Creo Illustrate is a good example.
Parametric Modeling Cad Tutorial
PTC began developing Creo in 2009, and announced it using the code name Project Lightning at PlanetPTC Live, in Las Vegas, in June 2010.[2] In October 2010, PTC unveiled the product name for Project Lightning to be Creo.[3] PTC released Creo 1.0 in June 2011.[4]
Creo apps are available in English, German, Russian, French, Italian, Spanish, Japanese, Korean, Chinese Simplified, and Chinese Traditional. The extent of localization varies from full translation of the product (including Help) to user interface only.
Creo is part of a broader product development system developed by PTC. It connects to PTC's other solutions that aid product development, including Windchill for Product Lifecycle Management (PLM), Mathcad for engineering calculations and Arbortext for enterprise publishing software.
Version | Release date |
---|---|
Creo 1.0 | 6 January 2011 |
Creo 2.0 | 27 March 2012 |
Creo 3.0 | 17 March 2014 |
Creo 4.0 | 15 December 2016 [5] |
Creo 5.0 | 19 March 2018 [6] |
Creo 6.0 | 19 March 2019 |
Creo 7.0 | 14 April 2020 |
See also[edit]
References[edit]
- ^Software Update Availability (Advanced)Archived 2016-03-04 at the Wayback Machine
- ^Reflections on PTCUser ConferenceArchived 2012-03-23 at the Wayback Machine, Tech-Clarity, 14 June 2010.
- ^PTC Reveals Project Lightning as Creo, Desktop Engineering, 28 October 2010.
- ^PTC Releases Creo 1.0, Tenlinks.com, 13 June 2011.
- ^'PTC Announces Creo 4.0 for Smarter Design'. Business Wire. 15 November 2016.
- ^'PTC Announces Creo 5.0, the Latest Version of its Award-Winning CAD Solution'. 19 March 2018.
External links[edit]
The AEC world has long debated over parametric vs direct modeling. Both approaches have their own virtues and shortcomings which often lead to a frequent question for beginners: Should I choose Parametric Modeling or should I go for Direct modeling? BluEntCAD decided to pick up its thinking hat and explore more. Read on to find out what we understood from our own experience!
Table of Contents:
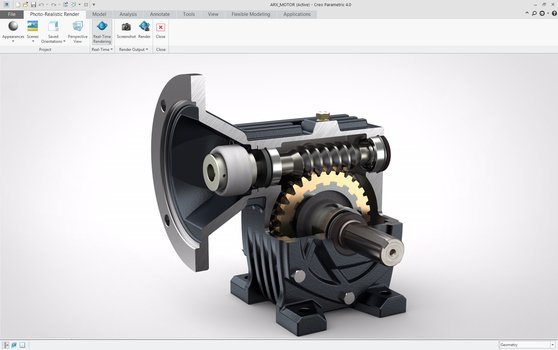
- What is parametric modeling?
- What is direct modeling
Many engineers like the flexibility and freedom which comes with direct modeling whereas feature definition and capability to control dimensions make parametric modeling preferred medium for others.
Direct modeling software
Direct modeling as the name suggests, is truly direct. Pretty straightforward and to-the-point. You can capture and define geometry quickly without worrying about constraints, features an original design intent.
Direct modeling is as simple as it gets.
Parametric modeling technologies
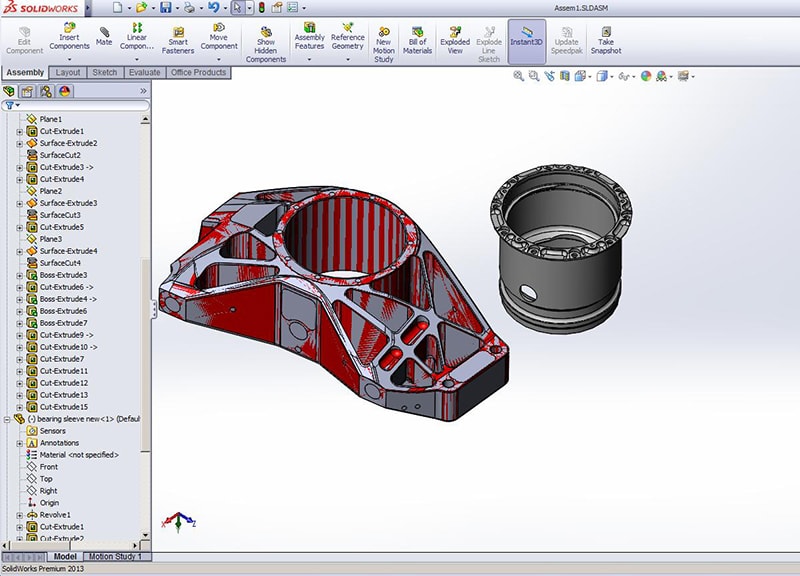
- What is parametric modeling?
- What is direct modeling
Many engineers like the flexibility and freedom which comes with direct modeling whereas feature definition and capability to control dimensions make parametric modeling preferred medium for others.
Direct modeling software
Direct modeling as the name suggests, is truly direct. Pretty straightforward and to-the-point. You can capture and define geometry quickly without worrying about constraints, features an original design intent.
Direct modeling is as simple as it gets.
Parametric modeling technologies
For those of us who like taking their own sweet time with designs, parametric modeling software is the answer. Whenever designers need to capture design intent complete with constraints and features, parametric modeling is used. Since you command a better control, you can automate changes which are repetitive; making parametric modeling convenient.
Okay.
So? Which is better?
What should I choose for my next project? Parametric modeling architecture or direct modeling?
There is no right or wrong approach. In fact, best CAD software and CAD experts use both approaches to model.
The result? Best of both worlds!
Designers and manufacturers who integrate direct modeling to parametric modeling report better quality, enhanced speed and higher focus on innovation to keep them a step ahead of their competition.
Let's dive deeper into parametric modeling CAD and direct modeling CAD.
What is parametric modeling?
Any model geometry is known to be parametric if the shape of the object changes as soon as the dimension value is modified. Parametric modeling utilizes computer-aided design to create systems and objects which model component attributes with real-life response.
By using this type of modeling, various design variables become easy to manipulate; in order to create diverse permutations for a single design.
With parametric modeling, designs have the potential to be ever-changing and flexible. This approach has the potential to transform the entire design process because designer intent and ideas are close-knit.
Parametric 3d Cad
Why is parametric modeling used?
Parametric modeling is generally used in projects where designers are directly involved in how building (designed by them) is going to be constructed and how it will be projected to the entity who is going to work on the final project.
Parametric designing is the creation of digital models which are based on series of algorithms called as parameters. This means that the model's elements are generated automatically using internal decision making of the CAD software rather than manual adjustments.
Let's understand this with an example. You want to ensure that the walls of your room should begin at the floor level and should reach the ceiling underside. In this case, if the ceiling to floor height changes, the walls will adjust accordingly. English movie 6. Now that your algorithm is designed, you can use it throughout the model.
Who uses parametric modeling?
The history of architecture shows that the modeling has been used on specialized designing tasks. The Beijing National Stadium and Shanghai Tower bear testimony to using parametric designing techniques.
This kind of modeling is also used in structural analysis for processing complex geometric rules like panel layout of curvilinear forms and fabrication rules. However, a major chunk of parametric modeling in mainstream building construction design has been brought by BIM or Building Information Modeling. While BIM software generally uses object definition to create designs, it can still use parametric attributes such as colors, dimensions, positional data, manufacturer's data and so on.
For instance, if your project has color attribute then every object that has color attribute will change if the color scheme for your building changes.
What is direct modeling?
Direct modeling allows CAD designers to interact directly with model geometry. This means they can manipulate an object's geometry by pulling, twisting or pushing. Contrary to parametric modeling where you need to create the final model in steps, direct modeling allows geometry of the features to be modified without the need to edit interim model stages.
Why use Direct modeling?
Direct modeling offers a ‘just do it' approach with its ability to quickly define and capture geometry. Rather than creating constraints, building features and design intent to your model, you can instead focus on creating geometry.
Direct modeling favors responsiveness towards change, for making design strategies where flexibility and speed are key.
Both parametric and direct modeling has several virtues and features. Let's take a look at their unique features and shortcomings so that you make better informed decisions.
Advantages and disadvantages of Parametric Modeling
Why-Use-Direct-modeling tools are conducive for design tasks which involve strict criteria for manufacturing objects on a continuous basis.
Pros of Parametric Modeling
- Automatic model updates whenever new changes are made
- Easy capture of design intent for defining the behavior of the model conveniently
- Automatic family creation
- Superb integration with manufacturing processes; thereby resulting in decreased production time
Cons of Parametric Modeling
Parametric Modeling Cad
- Parametric 3D Modeling can become heavy-handed during concept design; especially when designers are still exploring ideas
- Updates take more time in parametric models in case of last-stage design changes
Advantages and disadvantages of direct modeling
Since direct modeling creates geometry instead of features, the designer is not bogged down with features and their respective inter-dependencies. It is all about having flexibility, speed and agility in the design process.
Pros of direct modeling
- Quick and easy creation of new 3D models
- Ability to make amends with ease
- Almost no design automation
- Weaker dimension oriented editing
So, what does this mean for the users?
The ideal solution for successful and feature rich projects is a blended approach. Experienced designers such as our CAD experts are able to leverage the best of both parametric and direct modeling techniques without being limited by their shortcomings.
Parametric Cad Program
At BluEntCAD, our experts use full-featured modeling tools which utilize both parametric and direct modeling capabilities in a unified environment to create one model. You can know more about our projects by getting in touch with us via mail; call or form submission.
Maximum Value. Achieved.